Artykuł sponsorowany
Optymalizacja procesów galwanicznych dla osiągnięcia najlepszych rezultatów
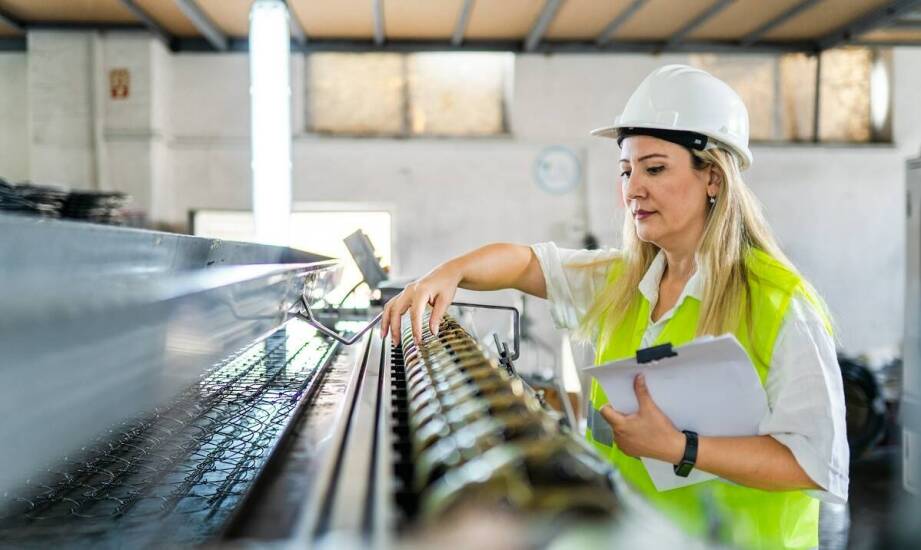
Galwanotechnika to dziedzina przemysłu, która ma kluczowe znaczenie dla wielu sektorów, takich jak motoryzacja, elektronika czy budownictwo. Procesy galwaniczne pozwalają na pokrywanie powierzchni metali cennymi lub innymi metalami, co zwiększa ich trwałość, odporność na korozję oraz poprawia wygląd. Optymalizacja tych procesów jest kluczowa dla osiągnięcia najlepszych rezultatów, zarówno pod względem jakości produktu, jak i efektywności kosztowej. W tym artykule przedstawimy cztery aspekty optymalizacji procesów galwanicznych.
Kontrola jakości i monitorowanie procesu
Pierwszym krokiem w procesie takim jak optymalizacja procesów galwanicznych jest zapewnienie odpowiedniej kontroli jakości i monitorowania procesu. W tym celu należy stosować odpowiednie metody badawcze, takie jak analiza składu chemicznego, pomiar grubości powłoki czy ocena właściwości mechanicznych i korozyjnych. Ponadto, ważne jest również ścisłe monitorowanie parametrów procesowych, takich jak temperatura, czas trwania czy stężenie elektrolitu. Dzięki temu możliwe jest szybkie wykrywanie ewentualnych odchyleń od normy i wprowadzenie niezbędnych korekt.
Odpowiedni dobór elektrolitu i parametrów procesu
Kolejnym istotnym elementem optymalizacji procesów galwanicznych jest odpowiedni dobór elektrolitu oraz parametrów procesu. Elektrolit powinien być dobrany tak, aby zapewnić równomierne osadzanie metali na powierzchni, a także minimalizować ryzyko wystąpienia defektów, takich jak pęcherze powietrza czy nierówności. Parametry procesu, takie jak napięcie, prąd czy czas trwania, muszą być dostosowane do konkretnego materiału i wymagań jakościowych. Warto również zwrócić uwagę na optymalizację kształtu anod i katod, co może wpłynąć na jednorodność powłoki.
Zarządzanie odpadami i ochrona środowiska
Procesy galwaniczne generują dużą ilość odpadów, zarówno stałych, jak i ciekłych. Odpowiednie zarządzanie tymi odpadami oraz dbałość o ochronę środowiska są niezbędne dla zrównoważonego rozwoju przemysłu galwanotechnicznego. Należy stosować technologie pozwalające na minimalizację ilości generowanych odpadów, takie jak odzysk metali czy recykling elektrolitów. Ponadto, ważne jest również monitorowanie emisji do powietrza oraz stosowanie odpowiednich systemów oczyszczania ścieków.